Understanding Automotive Injection Molds: A Key Component in Metal Fabrication
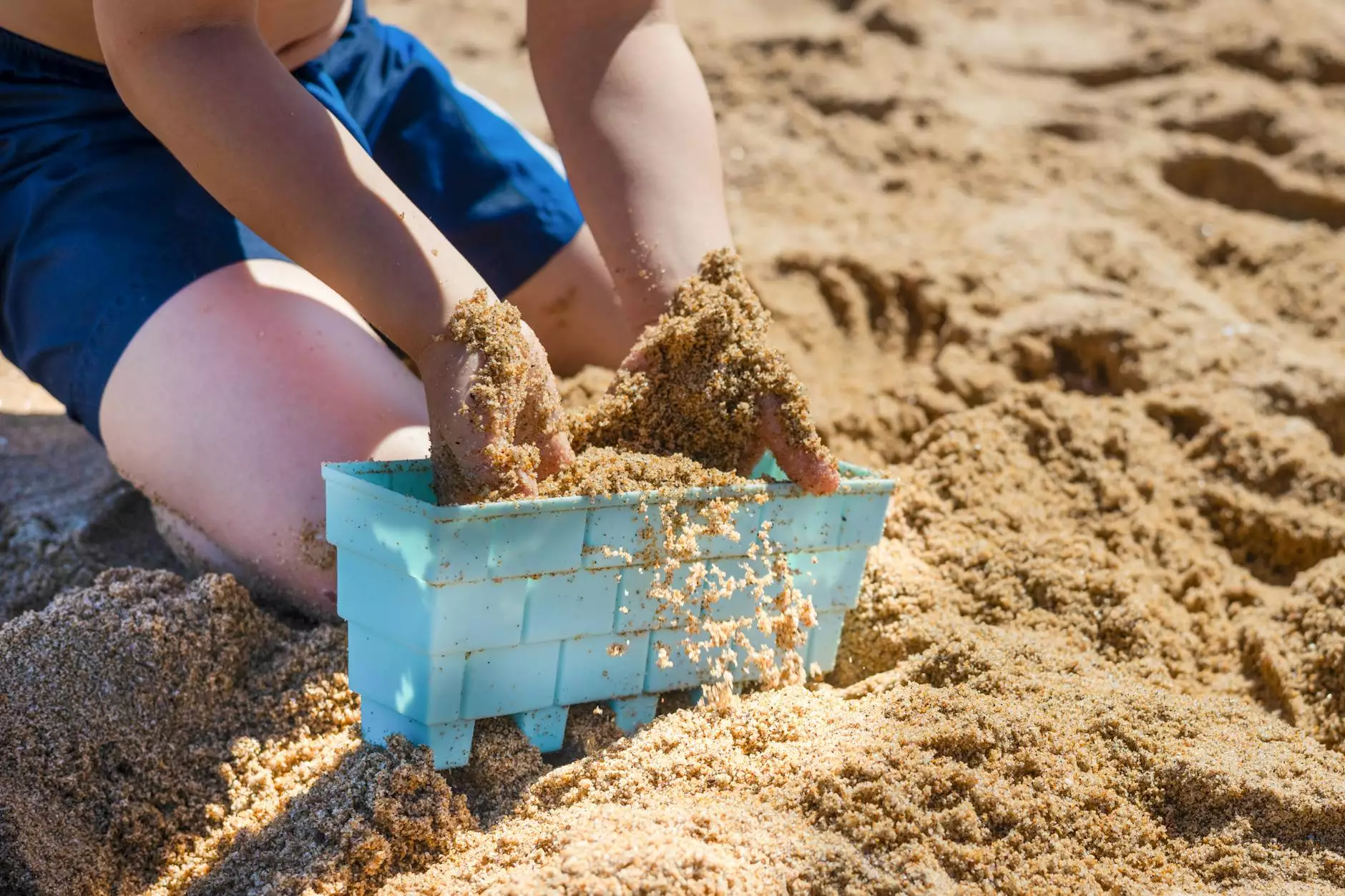
The automotive industry is a cornerstone of the global economy, known for its constant innovation and rigorous efficiency standards. One of the unsung heroes in this industry is the automotive injection mold, a crucial element in the production of various car parts. In this article, we'll delve deep into the significance of automotive injection molds within the realm of metal fabrication, exploring their benefits, applications, and the latest advancements in technology.
What is an Automotive Injection Mold?
An automotive injection mold is a tool used to create parts through the injection molding process—where molten material is inserted into a mold cavity to form specific shapes. This method is particularly vital in the automotive industry as it allows for the production of highly complex components with precision and repeatability.
Key Components of an Injection Mold
The components that make up an automotive injection mold include:
- Cavity: The part of the mold that gives shape to the final product.
- Core: The core works in conjunction with the cavity to define the internal dimensions of the part.
- Runner system: Pathways through which the molten material is channeled into the mold.
- Cooling system: Circulates cooling fluids to help the part solidify and reduce cycle times.
- Ejector system: Mechanism that ejects the molded part from the cavity once it has solidified.
Importance of Automotive Injection Molds
Automotive injection molds play a pivotal role in ensuring that parts are manufactured efficiently and to the highest standards. Here are several reasons highlighting their importance:
1. Precision Manufacturing
Injection molding is an incredibly precise manufacturing process. It allows manufacturers to create detailed and complex parts that meet the tight tolerances required in automotive applications. This precision contributes to the overall performance and safety of vehicles.
2. Efficiency and Cost-Effectiveness
Automotive injection molds enable high-speed production of parts, drastically reducing manufacturing costs per unit. This efficiency is crucial for car manufacturers aiming to keep production expenses low while meeting market demands.
3. Material Versatility
Injection molding can accommodate a wide range of materials, including various plastics and metals. This versatility allows automotive manufacturers to select the best materials for specific applications, enhancing strength, durability, and aesthetics in their products.
Applications of Automotive Injection Molds
Automotive injection molds are used in a variety of applications within the automotive industry:
1. Interior Components
Many interior components of vehicles, such as dashboard panels, console covers, and door handles, are produced using automotive injection molds. These parts require intricate designs and finish, which the injection molding process can achieve effectively.
2. Exterior Parts
Injection molding is also employed for exterior components, including bumpers, grilles, and fenders. The process ensures that these parts are both lightweight and robust, contributing to the vehicle’s overall design and performance.
3. Mechanical Components
Automotive engines and mechanical systems often utilize parts made via injection molding. Components such as housings, brackets, and clips benefit from the precision and strength provided by this method, ensuring optimal performance under stress.
Advancements in Automotive Injection Molding Technology
The world of automotive manufacturing is continually evolving, and with it, the technology surrounding automotive injection molds. Here are some of the latest trends and advancements:
1. 3D Printing and Prototyping
3D printing technologies are revolutionizing the design process for injection molds. Rapid prototyping allows manufacturers to create and test molds quickly, reducing lead times and enhancing creativity in design.
2. Smart Molding Processes
Integrating IoT technologies into injection molding processes allows for real-time monitoring and data analysis. This capability facilitates predictive maintenance, reducing downtime and improving overall production efficiency.
3. Sustainable Practices
The automotive industry is moving toward more sustainable manufacturing practices. Innovations such as bio-based materials for molds and recycling processes are becoming standard as companies seek to lower their environmental impact.
Challenges Facing the Injection Mold Industry
Despite its numerous advantages, the automotive injection mold industry faces several challenges that need to be addressed:
1. High Initial Costs
The design and manufacturing of injection molds can entail significant upfront costs, which may pose a barrier for smaller manufacturers looking to enter the market.
2. Demand for High-Quality Standards
As the automotive industry continues to advance, so too do the quality standards expected of manufacturers. Keeping pace with these standards requires ongoing investment in technology and training.
3. Skilled Labor Shortage
Finding skilled labor in the injection molding sector can be challenging. Companies may need to invest in training programs or collaborate with educational institutions to cultivate a skilled workforce.
Conclusion
In the ever-evolving landscape of the automotive industry, automotive injection molds stand out as a vital component of modern manufacturing. They provide precision, efficiency, and versatility, enabling manufacturers to create high-quality automotive components that meet stringent standards.
As technology continues to advance, the opportunities within the injection molding sector are expanding. From incorporating smart manufacturing technologies to adopting sustainable practices, the future of automotive injection molds is bright.
With ongoing innovation and efficiency improvements, companies in the automotive industry, such as DeepMould.net, are well-positioned to leverage the power of injection molding in their production lines. By embracing these advancements, manufacturers can enhance their competitiveness and contribute to a sustainable future in automotive production.